Technique
Pate de Verre
|
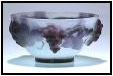
|
For a brief history of pate de verre and kiln
casting, click here. |
|
Pate de verre, or paste of glass, the
technique of pressing
glass powders or frits, crushed glass the consistancy of sand, into a
mold, is a detailed and difficult form of
kiln casting. However, it is the use of these fine frits that give pate
de verre its distinctive luster and allows for specific placement of
colors in the mold.
Pate de verre utilizes the 'lost wax' casting method that
other art objects are made of, from bronze sculpture to gold and silver
jewelry.
|
|
|
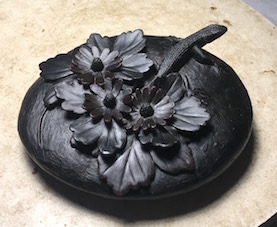
|
Each piece starts with a wax model. The model
can be an original carving or a duplicate made from a reproduction mold
that is poured around the original carving or object.
A model is an exact replica of the finished piece and can take anywhere
from a couple of hours to 15 or 20 or more to construct and/or carve
depending on how big and complex it is.
|
|
|
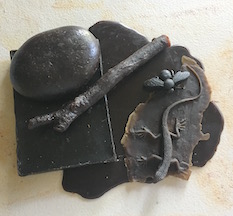
|
I use wax for my models as opposed to other
materials that
molds can be made from because my work has undercuts which make it
impossible to remove the model without damaging the mold.
I use a microcrystalline wax which is a dark brown that looks very much
like chocolate and contruct my models by pouring the melted wax into
shapes or sheets or small reproduction molds, combining elements,
carving and smoothing and polishing using a variety of tools.
|
|
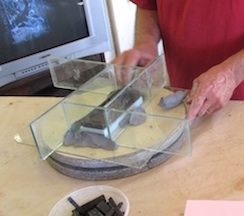
|
When the model is ready, it is glued down
onto a surface so it won't float and a dam or cottle is constructed
around it. This can be any water resistant material like plywood or
sheet metal or clay but we generally use pieces of plate glass because
we have a lot of that around here.
All the seams need to be sealed to prevent the investment, the
plaster/silica mold material, from leaking out when it is poured around
the model. |
|
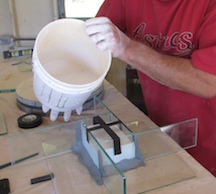
|
Pouring the investment. It takes about an
hour for it to set up.
|
|
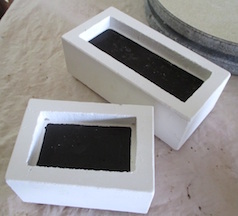
|
When the investment is set, the dam is
removed. The wax model is now encased in the plaster/silica investment. |
|
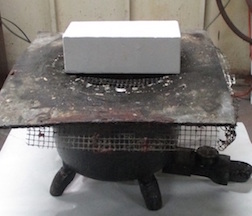
|
The wax model is then steamed out of the
mold, hence the term
'lost wax'. At this point the model is gone forever and the mold is
ready to be cleaned up and repaired if necessary. |
|
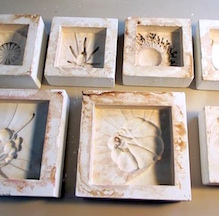
|
The molds are now ready to fill with glass
powders and frit.
|
|
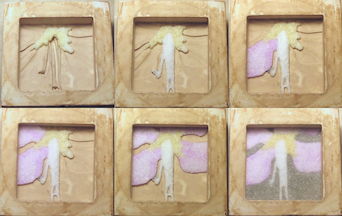
|
The
volume/weight of
glass required to fill the mold is calculated and the colors are
selected and weighed out into appropriate amounts. Frit crushed glass
about the consistancy of powder or fine sand is mixed with a binding
agent, we use a dilute solution of gum arabic, to form a sort of glass
paste and the colored frit is placed
selectively into the mold with small spoons, scoops, and spatulas.
|
|
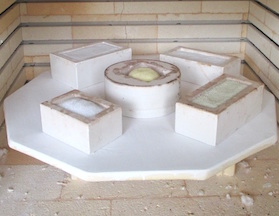
|
After
all the glass has been placed in the mold, it is set in
the kiln and slowly brought up to casting
temperature, 1400 - 1550 degrees, where it stays until the glass has
melted and filled all the negative spaces in the mold. After the hold
at casting temperature, it is reduced to the annealing
temperature where it must rest awhile. Finally the kiln is slowly
cooled over a period of many hours or days - the larger the piece, the
longer it takes. If the kiln is heated too fast, the mold will crack
and the molten glass will run out, if it is cooled down too rapidly,
the piece will
crack. When the kiln has returned to room temperatue, it can be removed
from the kiln. |
|
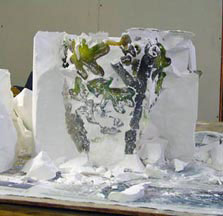
|
After firing the mold material, which now is
soft like chalk, is carefully removed from the cast glass and the piece
is washed. |
|
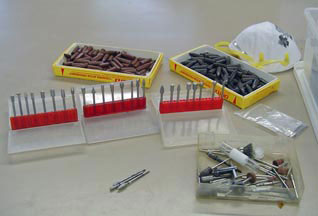
|
The amount of cold work required varies with
the
piece and depends on how well it cast among other considerations.
Excess glass is ground off using a flat lap. Finally, sharp points and
rough spots are removed with
diamond grinding bits and the surface is smoothed out with grit
impregnated polishing points. |
|